Site: Home > News and events
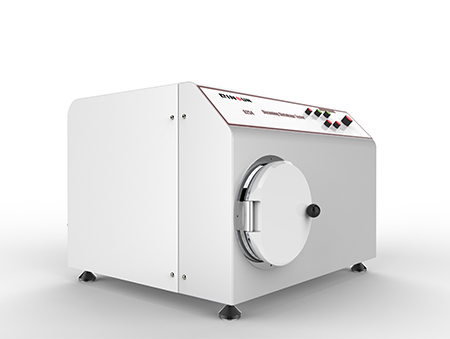
What are the 5 different types of textile elastic fibers?

Among many textile products, textile elastic fibers can give the human body a good sense of contact, and play an irreplaceable role in the wearing comfort and shape retention of clothing. Therefore, they occupy a stable position in textile fibers. Certain elasticity of textile fabrics has become an inevitable development trend of clothing textiles.
What are the 5 different types of textile elastic fibers?
1. Diene textile elastic fiber (rubber yarn)
Diene textile elastic fiber is commonly known as rubber yarn or elastic yarn. The main chemical component is vulcanized polyisoprene. It has good chemical and physical properties such as high temperature resistance, acid and alkali resistance, and abrasion resistance. It is widely used in socks and ribs. Knitting industry such as cuffs. Rubber thread is a textile elastic fiber used in the early days. Because it is mainly made into coarse yarns, its use in woven fabrics is very limited.
2. Polyurethane fiber (spandex)
Polyurethane textile elastic fiber refers to a fiber made of a block copolymer with polyurethane as the main component. my country is referred to as spandex. The original trade name in the United States is Spandex, which was later renamed Lycra Lycra, and Elastane in Europe. It is called Neolon in Japan and Dorlastan in Germany. Its elasticity comes from its molecular structure consisting of so-called "soft" and "hard" segments of the block copolymer network structure.
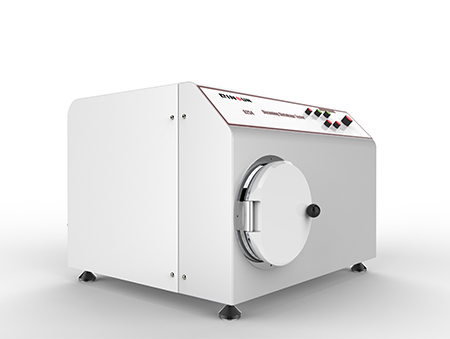
Spandex spinning methods include dry spinning, wet spinning, chemical reaction spinning and melt spinning. Dry spinning technology is currently the most common method of spandex industrial production. Spandex is an earlier developed and most widely used variety of textile elastic fibers with the most mature production technology. The performance of spandex textile elastic fiber is better than that of rubber silk textile elastic fiber.
3. Polyetherester textile elastic fiber
Polyetherester textile elastic fiber is a textile elastic fiber made of polyester and polyether copolymer through melt spinning. It was first produced in 1990 by Teijin Corporation of Japan. Polyetherester textile elastic fibers are similar in structure to polyurethane textile elastic fibers, and they also have "segment" structural characteristics. The "soft" segment is mainly polyether segment, which has good flexibility, longer chain, and easy to stretch and deform; the "hard" segment is a polyester segment, which is relatively rigid and easy to crystallize. The chain is short. It acts as a node when deformed by force, imparts elastic recovery performance, and determines the strength and heat resistance of the fiber.
Polyetherester textile elastic fiber not only has high strength, but also good elasticity, and has a high melting point. It can be blended with PET fiber and can be dyed at 120~130 ℃, so polyester fiber can also be processed into elastic textile. In addition, their light resistance is excellent, chlorine bleaching resistance, acid and alkali resistance, etc. are better than ordinary spandex.
This kind of fiber also has the advantages of cheap raw materials, easy production and processing, and it is a kind of more promising fiber.
4. Composite textile elastic fiber (T400 fiber)
CONTEX (ST 100 composite textile elastic fiber, collectively referred to as T400 textile elastic fiber in the market) is a two-component new composite elastic fiber that uses DuPont Sorona as the main raw material and is made with ordinary PET through advanced composite spinning technology; Permanent spiral crimp and excellent bulkiness, elasticity, elastic recovery rate, color fastness and particularly soft hand feeling, it can be woven alone or interwoven with cotton, viscose, polyester, nylon, etc. to form a variety of The kind of style.
It not only solves the problems of traditional spandex yarns that are not easy to dye, excessive elasticity, complex weaving, unstable fabric size, and easy aging during use, but also can be woven directly on air jet, water jet, arrow shaft looms, and does not need to be like spandex. In that way, it must be made into covered yarn before weaving on the machine, which reduces the cost of yarn and improves the quality uniformity of the product.
5. Polyolefin textile elastic fiber (DOW XLA fiber)
Polyolefin textile elastic fiber is made by melt spinning of polyolefin thermoplastic elastomer. XLA, launched by DOW Chemical in 2002, is the first commercialized polyolefin textile elastic fiber. It is made by melt-spinning an ethylene-octene copolymer (POE) catalyzed by a metallocene catalyst for in-situ polymerization. have to.
It has good elasticity, 500% elongation at break; can withstand high temperatures of 220 ℃; resistant to chlorine bleaching and strong acid and alkali treatment; and has strong resistance to ultraviolet degradation. Its production process is relatively simple, the price of raw materials is lower than that of spandex, and at the same time, there is almost no pollution during the production process and it is easy to recycle. As polyolefin textile elastic fibers possess a variety of excellent properties, they have become increasingly widely used in recent years.
Want to learn more about textile products? Take a look at the qinsun website, our textile testing equipment will escort your textile products!
2021-09-03 14:04
- Related News
VP-TEST-5000: Transpiration Analyzer for Textiles
DPL-2000: Steady-State Thermal Conductivity Tester
HTC-3000: Thermal Conductivity Analyzer for Extreme Environments
Flammability Analyzer by Oxygen Index
TRACKING-8000: Electrical Insulation Tracking Analyzer
MELTINDEX-3000: Polymer Flow Rate Analyzer
Color Fastness Tester Resistant to Scrub
CHRYSLER-BEND-5000: Automotive Component Flexibility Analyzer