Oil Mist Separator Test System
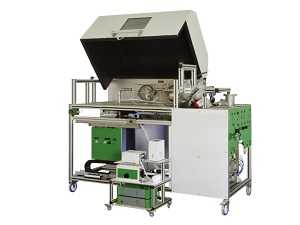
The test rigs purpose is the testing of oil mist separators re capture rate, flowrate curve (pressure loss relative to flowrate), pressure regulation curve and leakage. The unit to be tested will be fed with an oil aerosol (flowrate and temperature adjustable) either in positive or negative pressure conditions. The immediate vicinity of the filter is temperature controlled. During the collection efficiency measurement the separated and the let-to-pass oil amounts are measured in dependence on the volumetric flow. They are automatically recorded, applying the gravimetric method, by means of an absolute filter. The amount of oil leaving the separator can be recorded online. Additionally, the leakage of the oil drain valve can be measured. The test rig simulates the operating conditions in typical fields of oil aerosol separator application. When recording the pressure control characteristic, the „pressure in the crankcase“ is simulated in dependence on the „suction pipe pressure“ for different flow rates.
Features
◆ Wide range of flow rate for overpressure and underpressure operation mode
◆ Special operating mode for testing pressure control valves
◆ Sample holder adjustable for different sample dimension
◆ Heatable test chamber (ambient temperature up to 120°C/248°F)
◆ Closed loop test air recovery system (with cooling stage)
◆ Aerosol generation by means of ATM 243 and/or LDG 244
◆ Safe test chamber with hinged cover
◆ Software guided testing procedure
◆ Convenient Windows software for test rig control, data acquisition and data export
Test chamber (opened) with upstream and downstream test piece connectors, being adjustable for different test object sizes. Integrated in the rear plate the heater blower combination
Design
The test rig consists of:
* a volumetric flow unit to implement varying volume flows in overpressure or underpressure mode
* a specially configured aerosol generator
* a facility for gravimetric collection efficiency measurement
* a multitude of sensors and controllers for the measurement of temperature and differential pressure
* switch box, rack and test rig control
The test rig requires certain media supply connections as electric power, pressurized air and cooling water connecting lines. The cooling system permits either to emit the exhaust air in a common discharge system or to conduct a recalculated air operation. It is recommended to connect to an exhaust system for safety reasons.
A special technical solution applying a backup filter was developed to allow the determination of the separation performance of the unit under test over a determined period under constant test conditions. Two filters, each of them separately replaceable, are alternately connected. In the start-up period initially the first filter is used until the test conditions do not vary anymore. For the measurement itself it is changed over to the second filter.
Features
◆ Wide range of flow rate for overpressure and underpressure operation mode
◆ Special operating mode for testing pressure control valves
◆ Sample holder adjustable for different sample dimension
◆ Heatable test chamber (ambient temperature up to 120°C/248°F)
◆ Closed loop test air recovery system (with cooling stage)
◆ Aerosol generation by means of ATM 243 and/or LDG 244
◆ Safe test chamber with hinged cover
◆ Software guided testing procedure
◆ Convenient Windows software for test rig control, data acquisition and data export
Test chamber (opened) with upstream and downstream test piece connectors, being adjustable for different test object sizes. Integrated in the rear plate the heater blower combination
Design
The test rig consists of:
* a volumetric flow unit to implement varying volume flows in overpressure or underpressure mode
* a specially configured aerosol generator
* a facility for gravimetric collection efficiency measurement
* a multitude of sensors and controllers for the measurement of temperature and differential pressure
* switch box, rack and test rig control
The test rig requires certain media supply connections as electric power, pressurized air and cooling water connecting lines. The cooling system permits either to emit the exhaust air in a common discharge system or to conduct a recalculated air operation. It is recommended to connect to an exhaust system for safety reasons.
A special technical solution applying a backup filter was developed to allow the determination of the separation performance of the unit under test over a determined period under constant test conditions. Two filters, each of them separately replaceable, are alternately connected. In the start-up period initially the first filter is used until the test conditions do not vary anymore. For the measurement itself it is changed over to the second filter.
Note:QINSUN is very in place for textile testing and quality control,we have our own textile testing lab. Our textile testing equipment and testing methods are in the leading position in the industry. We have passed the textile testing certification and iso textile testing standards issued by a number of testing,We can provide textile testing equipment pdf manual. Sufficient inventory, big discounts, limited time promotion, Order now!
Leave Message Get Price