Coating Shear Fatigue Tester
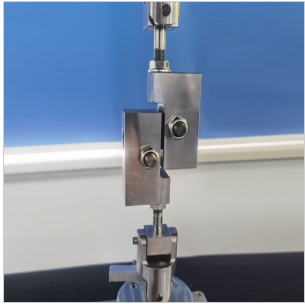
Standards:
ASTM F1044
ASTM F1160
ASTM D5617
ASTM D6188
Scope of Application:
The Coating Shear Fatigue Tester is used to apply a repetitive shear force to a coating applied to a substrate. This cyclic shearing action simulates the stresses a coating might experience in various real-world applications, such as in automotive coatings subjected to vibration and thermal cycling, coatings on medical implants experiencing physiological loading, or industrial coatings exposed to dynamic stresses. The test evaluates the coating's ability to withstand these cyclic shear forces without failure, providing vital data for:
Coating material research and development: In the research and development stage of coating materials, this tester can be used to evaluate the influence of different formulations, processes, and additives on the fatigue performance of coatings, so as to optimize the design and preparation processes of coating materials for improved durability and adhesion under dynamic shear.
Coating quality control: During the production process, use the coating shear fatigue tester to conduct quality control inspections on coatings, ensuring that coating products meet the predetermined performance standards for shear fatigue resistance. This helps maintain consistency in manufactured coatings and predict their reliability in service.
Coating performance evaluation: For coatings that have been applied in actual products, this tester can be used to evaluate their fatigue life and durability under specific simulated service conditions. This can provide scientific evidence for predicting the remaining service life of a coating, informing maintenance schedules, and guiding product replacement decisions.
Product Advantages:
The Coating Shear Fatigue Tester offers significant advantages for evaluating the critical shear fatigue performance of coatings:
Evaluates a Key Failure Mode: Directly assesses the coating's resistance to shear fatigue, a common mechanism leading to delamination and degradation.
Provides Crucial Fatigue Life Data: Determines the number of cycles to failure at specific shear stress levels, essential for predicting long-term coating durability.
Supports Coating R&D: Enables researchers to optimize coating formulations and application processes for enhanced fatigue resistance.
Essential for Quality Control: Provides a standardized method for ensuring the consistent shear fatigue performance of manufactured coatings.
Simulates Cyclic Service Conditions: Replicates the repetitive shear stresses experienced by coatings in various applications.
Objective Performance Data: Yields quantitative measurements of fatigue life and shear deformation under cyclic loading.
Product Features:
A Coating Shear Fatigue Tester is typically a dynamic testing system configured to apply controlled cyclic shear loads to coated specimens. Key features include:
A dynamic testing frame (e.g., servo-hydraulic or electrodynamic) capable of applying precise cyclic loads in shear.
A specialized fixture designed to hold the coated specimen and apply cyclic shear stress to the coating layer. This might involve gripping the substrate and a superimposed layer or using a lap shear configuration where the coating is the bond between two substrates, with the fixture designed to induce shear fatigue in the coated interface. The fixture design is crucial for isolating and applying shear stress accurately.
A dynamic load cell for accurate measurement of the applied cyclic shear force.
A displacement sensor or the testing machine's measurement system to record the shear deformation or slip within the coated interface under cyclic loading.
Advanced control system capable of applying various cyclic waveforms (e.g., sinusoidal, haversine) at specified frequencies and shear load or displacement amplitudes.
A cycle counter to accurately record the total number of load cycles applied.
A data acquisition system to capture shear load, shear displacement, and cycle count data throughout the fatigue test.
Sophisticated software for setting up fatigue test parameters, real-time monitoring of test progress, detecting sample failure (e.g., coating delamination, cracking), and analyzing fatigue data (e.g., generating S-N curves, evaluating stiffness or deformation changes over cycles).8
(Optional) Environmental chamber or fluid bath if testing needs to be performed at temperatures or in environments relevant to the coating's application (e.g., high/low temperature, humidity, corrosive environments).
Safety features such as overload protection and automatic shutdown upon specimen failure.
Technical Parameters:
Dynamic Load Capacity (Shear): (e.g., typically ranging from ±0.1 kN to ±10 kN or more, depending on the expected shear strength of the coating and specimen configuration)
Frequency Range: (e.g., up to 10 Hz, 20 Hz, or higher, depending on the simulation requirements)
Load Control Accuracy: (e.g., ±1% of set load or better)
Displacement Control Accuracy: (e.g., ±1% of set displacement or better)
Type of Shear Application: (e.g., Single lap shear, double lap shear, or other specific fixture design)
Maximum Number of Cycles: (Designed for long-term testing, e.g., up to 1 million, 5 million, 10 million cycles, or more)
Actuator Stroke: (Sufficient to apply required shear displacements under cyclic loading)
Environmental Chamber/Fluid Bath Temperature Range: (If applicable, e.g., -40°C to +150°C or wider)
Environmental Chamber/Fluid Bath Control: (If applicable, temperature and potentially humidity or fluid circulation control)
Sample Size/Geometry Capacity: (Designed to accommodate standard coating test specimens, which vary depending on the standard and application)
Power Supply: (e.g., AC 220V or 380V, 50/60 Hz, potentially with a hydraulic power unit if servo-hydraulic)
Leave Message Get Price