The measurement of scratch to materials
Scratch testing is carried out to get an insight into materials to determine the resistance to abrasion and wear of modern composite materials and automotive paints varnishes, as well as coatings. Single asperity scratching allows the mechanisms behind abrasive or ductile damage of samples under investigation and the morphology of the scratches to be examined with a combination of microscopy and profilometry techniques. Scratch testing applications include commercial polymers, paint, and varnishes for the automotive industry, multilayered systems, and application-related performances
The test consists of applying a continuously increasing load on the coating surface by a hard metal or diamond spherical tipped indenter, typically of radius 200 μm, while the sample is displaced at a constant velocity. The scratching of the surface results in increasing elastic and plastic deformation until extensive spalling of coating from the substrate occurs at some critical load, Lc. The critical load is normally determined by optical microscopy, acoustic emission, or from friction force measurements. From measurement of the critical load the practical work of adhesion (Burnett and Rickerby, 1987, 1988; Bull et al., 1988) for a coating on substrate system can be obtained:
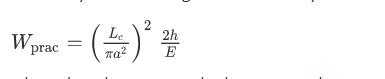
where h is the coating thickness, a is the contact radius, and E is the Young's modulus of the coating. This equation does not account for residual stress in the coating. In similar studies by Laugier (1984) for purely elastic coatings on stiff substrates, the practical work of adhesion is given by:

where σ is a function in the coating, which is determined by using σr the residual stress, and the applied stress, σappl (σ = σr + σappl). The residual stress in the coating is accounted for but the model is not entirely valid to describe the stresses when some plastic deformation occurs. Since these key studies, further developments to account for elastic stress distribution and residual stress in the coating have resulted in the following equation for determining strain energy release rate (Hutchinson and Suo, 1991; Venkataraman et al., 1993):

where σr is the residual stress, τij and σij are the average elastic shear and normal stresses in the delaminated coating, and μ is the shear modulus of the coating.
Overall, scratch testing needs to be approached with caution due to the complex stress states involved and the broad array of damage processes that can occur. Similarly other factors that need to be considered that can affect the test results include loading rate, scratching speed, tip shape, environment, and coating–substrate properties (hardness, roughness, thickness of the coating).
2019-08-16 18:04