Site: Home > News and events
The term “Fogging” refers to the film that collects on the inside of vehicle window glass. Of particular interest is the windshield, because this film can both limit light transmittal as well as refract the light that is transmitted, impairing visibility and creating safety concerns. A fogging test system is designed to determine the fogging value as defined in the various standards (see Table 1) as well as compare types of materials used in vehicle cabins.
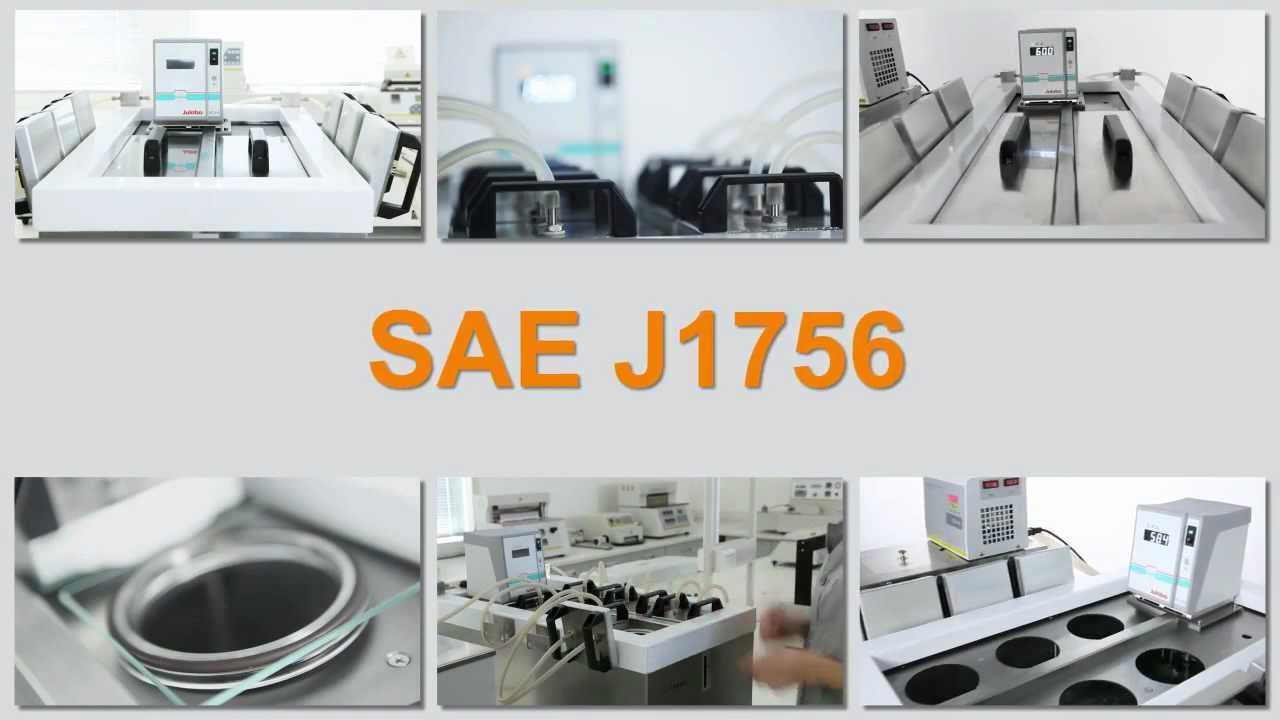
Test method for Fogging Tester

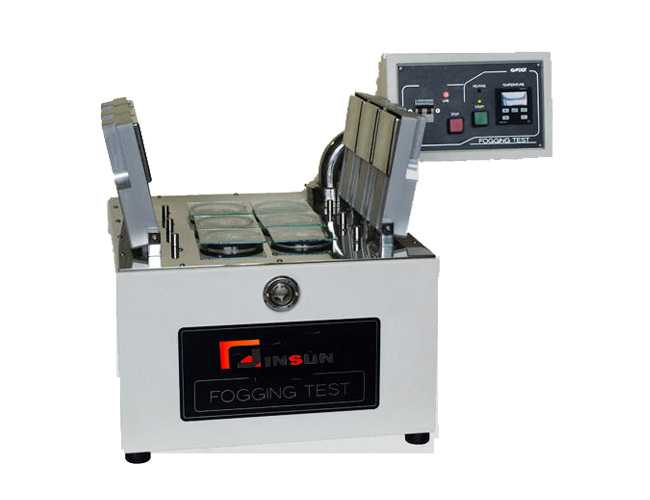
The term “Fogging” refers to the film that collects on the inside of vehicle window glass. Of particular interest is the windshield, because this film can both limit light transmittal as well as refract the light that is transmitted, impairing visibility and creating safety concerns. A fogging test system is designed to determine the fogging value as defined in the various standards (see Table 1) as well as compare types of materials used in vehicle cabins.
A new area for the fogging test within the automobile industry is HID (High Intensity Discharge) headlight components. HID lights operate at high temperatures in a micro-environment typically comprised of a polymer reflector and lense and the glass HID bulb.
The outgassed SVOCs re-condense on all surfaces of the bulb, reflector and lens when the HID light is turned off. The resultant film reduces light transmittal from all components and refracts or scatters the light in undesirable directions, potentially reducing night time visibility for the driver.
While fog testing was originally created for the automotive industry,there are other industries where this type of testing could prove useful.The concern for visibility, safety and the economic impact of SVOCs condensing on glass applies to any form of public transportation,recreational vehicles, aircraft, buses and trains.
The Methods:
The German Institute for Standardization has created the standard DIN 75201 that defines test procedures and conditions for fog testing in motor vehicles (i.e., automobiles, trains and planes) which determine the amount of undesirable evaporation and condensing of SVOCs from the material being tested.
Thermo Fisher Scientific supplies the test equipment required to measure fogging behaviors in accordance with the DIN, SAE and ISO standards (see Table 1).
The standards outline three methods for determining the fogging characteristics of interior materials in motor vehicles, marine and aircraft. The materials tested include plastic interior trim,polyurethane, textiles, leather,adhesives, elastomers, etc.
DIN 75201 as described below was the original standard for fog testing. Currently it is only in use for the testing of leather while various ISO and SAE standards,whose origins are based on DIN75201, are the current standards for polymers and polymer-coated fabric.
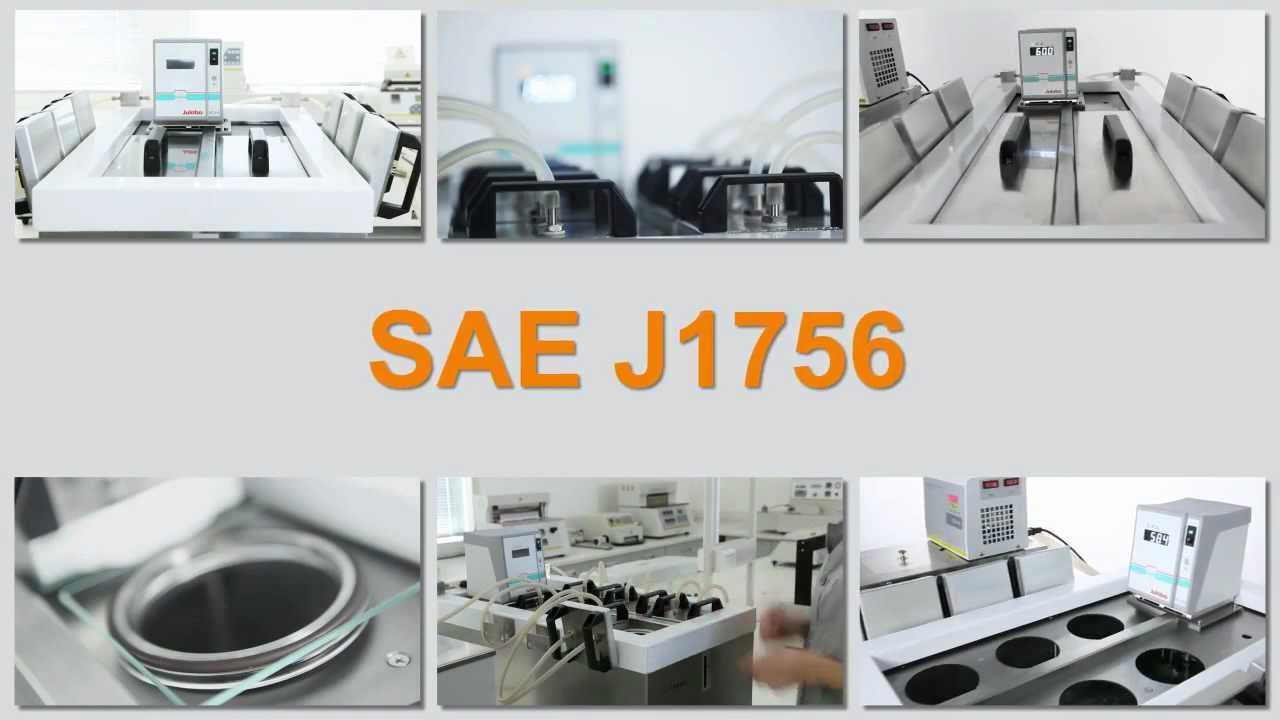
Fogging Behavior DIN 75201 Reflectometric method, photometric method:
fogging method, gloss method According to this method, a prepared sample is placed in a beaker that is then covered with a glass plate. The plate’s Reflective Index has been measured and recorded using a handheld reflectometer. For a period of three hours the sample is heated to 100°C, while the glass plate is cooled to 21°C. The heat causes the sample to release SVOC gasses that condense on the cooled glass plate creating a “Fog” (F). The Reflective Index of the fogged glass is measured and recorded.
Fogging value (Fv) is expressed as a percent of change in the 60° Reflective Index of a glass plate that has been fogged in accordance with the procedures (R1) to a clean glass plate (R2).
Fv = (R2 x 100)/R1
Where:
Fv = Fogging value
R1 = the mean initial reflective index of the glass plate with the fogging condensate R2 = the mean initial reflective index of the glass plate DIN specifies the maximum value for Fv in this test at 90%.
Fogging Behavior DIN 75201 Gravimetric method:
According to this method, a prepared sample is placed in a beaker that is then covered with an aluminium foil disk. The disk’s mass has been measured and recorded. For a period of sixteen hours the sample is heated to 100°C, while the aluminium foil disk is cooled to 21°C. The heat causes the sample to release SVOC gasses that condense on the cooled aluminium foil disk creating a“Fog” (F) that has a measurable mass (m). The amount of fogging condensate is determined by weighing the aluminium foil disk again after the test and subtracting the known mass of the same aluminium foil disk before fogging.
mF = m2 – m1
mF = the mass of the fog condensate collected during the test
m1 = the initial mass of the disc of aluminum foil (milligrams)
m2 = the mass of the disc of aluminum foil with the fogging condensate (milligrams)
This is the preferred method because the longer run time and simple measurements increase accuracy while minimizing errors inherent in the reflectometric method such as contaminated or damaged glass, using the incorrect side of the glass, or errors in measuring the reflective index.
Fogging Behavior DIN 75201-A Haze method:
The hazing method uses the same process as the reflectometric but instead of measuring the Reflective Index of the glass, a haze meter is used. The haze meter measures the light transmission through the glass plate both before and after the fogging process.
It is worth noting that the proprietary standards of individual companies often use different temperatures and time periods to achieve specific results. (See Table 2).
Conclusion:
The German Institute for Standardization worked with Thermo Fisher Scientific to develop the fogging test equipment used in the DIN 75-201 standard that determines the out gassing of materials in motor vehicles.
Over the years, derivatives of this standard have been created and are now used in various industries. Because of the consistent, repeatable results of the Thermo Scientific Horizon Fogging Test System, it continues to be the equipment of choice for every standard. While the effort to clean an individual automotive windshield is minimal, creating, identifying and utilizing materials that emit SVOCs at a reduced rate is key to public safety, reduced maintenance expenses, and the customer perception of a quality product.
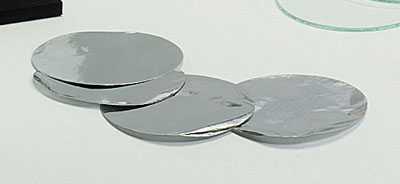
2019-03-22 15:21
- Related News
VP-TEST-5000: Transpiration Analyzer for Textiles
DPL-2000: Steady-State Thermal Conductivity Tester
HTC-3000: Thermal Conductivity Analyzer for Extreme Environments
Flammability Analyzer by Oxygen Index
TRACKING-8000: Electrical Insulation Tracking Analyzer
MELTINDEX-3000: Polymer Flow Rate Analyzer
Color Fastness Tester Resistant to Scrub
CHRYSLER-BEND-5000: Automotive Component Flexibility Analyzer