The RCA Abrasion Testing
For the RCA Test, temperature and humidity play an important role and must be reported; as well as, how the tested material and tape used were conditioned.RCA wear tests are significantly influenced by coating thickness and substrate material’s hardness;
The RCA abrasion testing specification, ASTM F2357, involves the use of a specific piece of testing equipment,.This RCA abrasion testing machine uses a small strip of abrasive paper, which is put into contact with the surface of the button for a specific number of cycles. A normal load is also applied throughout the test. Upon conclusion, an evaluation of the amount of visible wear is performed.
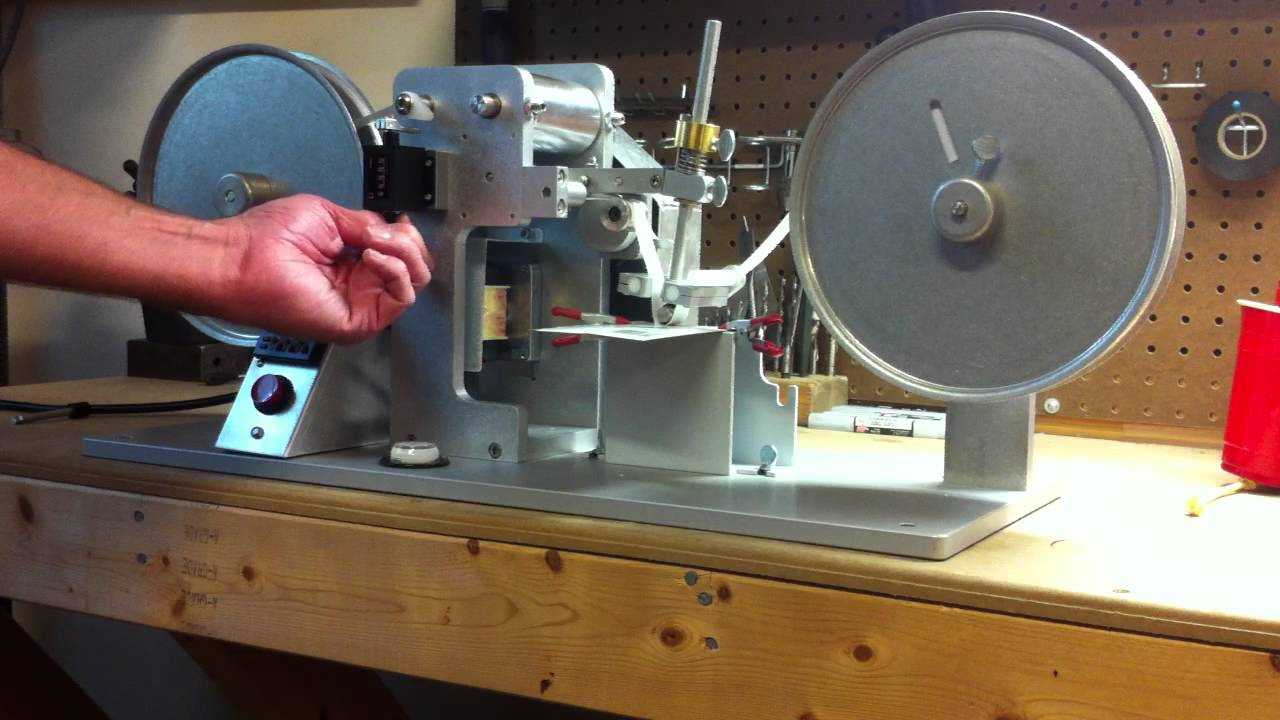
With both coatings tested it performedbetter higher dry film thickness.Higher functionality UV-cured coatings faired better than lower functionality.Temperature rise due to frictional heating with the corresponding change in the coefficient of friction, has an effect on the results of the test.The RCA wear test is significantly influenced by coating thickness and substrate material’s hardness.PMMA performed better than PC and both coatings performed better at higher dry film thickness.
In the Taber wear test the higher cross-linked coating performed better and the coating thickness had a positive effect. PC at the higher dry film thickness performed better. There is a minor difference in pencil hardness with increased coating thickness in thin films. However, there was a substantial difference based upon the substrate’s material hardness itself.
2018-09-07 17:03