Site: Home > News and events
8 important reference indicators in textile inspection reports

Many customers who do textile testing may have a question when they receive the test report from a third-party testing company: Is the test result of this textile good or bad? The qinsun tester manufacturer here will answer this doubt for you based on years of experience.
First of all, you must understand the content of the textile inspection report! In textile inspection reports,
there are 8 reference indicators that often appear:
1) Wear resistance
The test results of abrasion resistance are generally reflected in appearance changes, total friction times, and quality loss. The more commonly used method is to evaluate the wear resistance of the fabric based on the total friction times of the sample breakage. The more the times, the better the wear resistance of the fabric. For example, in GB/T 32614-2016 "Outdoor Sportswear Jackets", abrasion resistance is required to be ≥10000 times (the front of the fabric is not damaged); FZ/T 81006-2017 "Denim Clothing" is a qualified product with a weight of 339g/m2 or more. Requirement ≥20,000 times, 339g/m2 and below fabric requires ≥10,000 times.
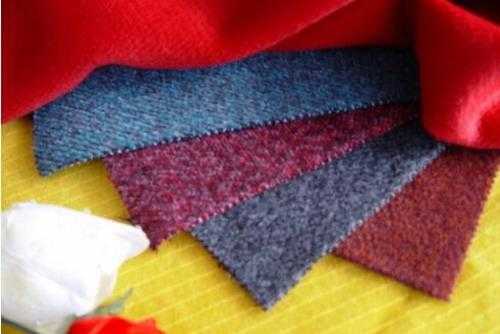
2) Anti-pilling
The results of the anti-pilling resistance test are generally expressed in grades. The higher the grade, the better the performance of the fabric against pilling. The rating is divided into 5 levels, with 5 being the best and 1 being the worst. In most product standards, the requirements for qualified products are level 3, while the requirements for products containing wool are lower. Generally, the requirements for first-class products are only level 3. Some products have exemptions, such as sanding and fleece. , Flocking, etc., do not require assessment by themselves.
3) Anti-drilling performance
The test result of anti-drilling performance is reflected by the number of down drilled. The more the number of roots, the worse the result, which means that the performance of the fabric to prevent the down from drilling is worse, and vice versa. Of course, the test methods are different, the results will be different, and there is no comparability between the methods. The current version of our common woven down garments GB/T 14272-2011 requires ≤50 pieces for qualified products, ≤15 pieces for first-class products, and ≤5 pieces for excellent products.
4) Three proofings—waterproof, oil proof, and dirt proof
Waterproof spray method, the test result is reflected in the water level, the highest level is 5. The higher the grade, the better the performance of the fabric against being wetted by water. For example, in GB/T 32614-2016 "Outdoor Sports Clothing and Jackets" Class I requirements, the requirements before washing are ≥ grade 4, and after washing, the requirements are ≥ grade 3.
The oil resistance test results are reflected in grades, up to 8.0. The higher the grade, the better the fabric's resistance to absorbing oily liquids. For example, in GB/T 21295-2014 "Technical Requirements for the Physical and Chemical Properties of Clothing", the finished product grade requirement is not less than 4.
Anti-fouling results are expressed in grades, and each method has different definitions for the evaluation of anti-fouling performance. For example: FZ/T 01118 has a description: when the initial color difference is equal to or lower than level 3, the color difference level of the test result is 3-4 and above, then the sample is considered to be easy to decontaminate; when the initial color difference is equal to or When it is higher than 3-4, the color difference grade of the test result is higher than the initial color difference 0.5 grade or more, then the sample is considered to be easy to decontaminate.
5) Waterproof hydrostatic pressure method
The test result is expressed by the hydrostatic pressure value of the sample (kPa/cmH2O/mmH2O). The larger the value, the better the fabric's resistance to water penetration. In the case of ready-to-wear garments, the seams and seamless parts will be assessed separately. For example, GB/T 32614-2016 "Outdoor Sportswear and Jackets" Class I requires before washing: fabric ≥50kPa, fabric seam ≥40kPa; after washing: fabric ≥40kPa, fabric seam ≥30kPa. (The conversion relationship between hydrostatic pressure units: kPa=10cm H2O=100 mmH2O)
6) Moisture permeability
The test result is reflected by the mass of water vapor passing vertically through the unit area of the sample within a specified time.
The unit is g/(m2.h) or g/(m2.24h). Generally speaking, moisture permeability is a measure of the moisture in the body. The higher the value, the more comfortable it is to wear. Therefore, it has a certain contradiction with hydrostatic pressure, which has exactly the opposite effect. In GB/T 32614-2016 "Outdoor Sportswear Jackets" Class I, it is required before washing: ≥5000 g/(m2.24h), after washing ≥4000 g/(m2.24h); while in FZ/T 81010-2018 "Windbreaker" has the same requirements for high-quality, first-class, and qualified products, and the uniformity is ≥5000 g/(m2.24h) regardless of whether it is washed before or after washing.
(The vapor and moisture permeability we usually hear on the market should reach 3000/3000 or 5000/5000, which refers to the requirements of hydrostatic pressure and moisture permeability.)
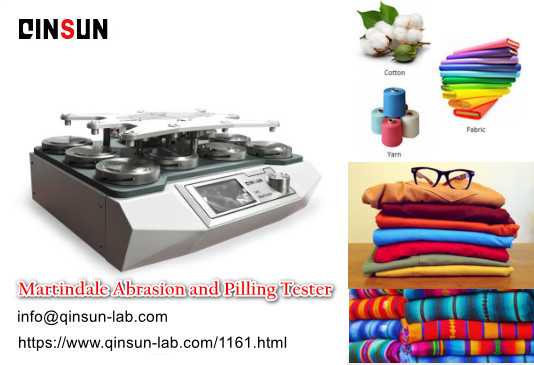
7) Air permeability
The test results are expressed in terms of the rate of air flow passing through the sample vertically (mm/s) under the specified test area, pressure drop and time conditions (mm/s), which represents the performance of air permeation through the fabric. Its results cannot be evaluated by numerical values alone, but by its end use. For example, the fabric used in summer needs to have better air permeability, while the outerwear worn in winter needs to be less air-permeable to ensure that the clothes have good wind resistance. Another example is the parachute fabric. If the air permeability value is too high, it may not be able to support a person's weight and fall down. If the value is too low, it may not fall down. Therefore, the air permeability is of great significance in the wearability of the fabric. In FZ/T 81010-2018 "Wind Coat", the air permeability is required to be ≤50 mm/s.
8) Anti-UV performance
The test results are reflected in the UV protection coefficient UPF, UV transmittance, and UV blocking rate. The content and requirements of different standards are different. Taking the national standard GB/T 18830 as an example, when the sample’s UV protection factor UPF>40 and the UV transmittance, T(UVA)AV<5%, it can be called a “anti-ultraviolet product”. One of these two conditions is missing. Not possible. UV protection products that meet these two conditions are marked as UPF 40+ when 40<UPF≤50; when UPF>50, they are marked UPF 50+.
Want to learn more about textile testing? Please leave us a message.web:https://www.qinsun-lab.com/
Want to learn more about textile testing? Please leave us a message.web:https://www.qinsun-lab.com/
2021-09-08 11:59
- Related News
VP-TEST-5000: Transpiration Analyzer for Textiles
DPL-2000: Steady-State Thermal Conductivity Tester
HTC-3000: Thermal Conductivity Analyzer for Extreme Environments
Flammability Analyzer by Oxygen Index
TRACKING-8000: Electrical Insulation Tracking Analyzer
MELTINDEX-3000: Polymer Flow Rate Analyzer
Color Fastness Tester Resistant to Scrub
CHRYSLER-BEND-5000: Automotive Component Flexibility Analyzer