Aluminum Tube Internal Coating Continuity Tester
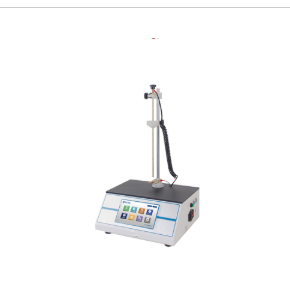
The continuity tester for the inner coating of aluminum tubes is an important device specifically used to detect the continuity of the inner coating of aluminum tubes. The following is a detailed description of its main uses, compliance standards, and technical parameters:
I. Main Uses
The continuity tester for the inner coating of aluminum tubes has extensive application value in multiple fields, and its main uses include: - **Quality Inspection**: During the production process of aluminum tubes, this tester can be used for the quality inspection of raw materials to ensure that the produced aluminum tubes meet relevant standards and requirements. Through testing, aluminum tubes with coating continuity defects can be promptly identified and removed, preventing unqualified products from entering the market. - **Product R & D**: In the product research and development stage, the continuity tester for the inner coating of aluminum tubes can provide important reference information for R & D personnel. By testing aluminum tubes produced under different formulations and processes, R & D personnel can evaluate the continuity and quality of the coating, thereby optimizing the formulation and process to improve product performance and competitiveness. - **Quality Control**: During the use of aluminum tubes, this tester can provide an important detection means for quality control departments. Through regular or irregular testing, the continuity and quality changes of the inner coating of aluminum tubes can be monitored, and potential quality problems can be identified and resolved in a timely manner, ensuring product stability and reliability.
II. Compliance Standards
The design and manufacture of the continuity tester for the inner coating of aluminum tubes usually comply with a series of national and international standards to ensure the accuracy and reliability of test results. Among them, common standards include YBB00162002 - 2015 *Aluminum Pharmaceutical Soft Tubes*, etc. These standards specify in detail the test methods, specimen preparation, test conditions, etc. for the continuity of the inner coating of aluminum tubes, providing a unified standard for the use of the tester.
III. Technical Parameters
- **Testing Range**: Applicable to aluminum tubes with a diameter between 8 and 45mm and a tube length between 35 and 250mm. This range covers most common aluminum tube specifications, giving the tester wide applicability. - **Testing Accuracy**: The testing accuracy is usually high. For example, the current measurement accuracy can reach ±0.1mA, etc. High - precision measurements can ensure the accuracy and reliability of test results, providing strong support for quality control and product R & D. - **Testing Voltage**: The testing voltage is usually adjustable within a certain range, such as DC 5V±0.5V, etc. By adjusting the testing voltage, it can meet the testing requirements of different coating materials and thicknesses, improving the flexibility and accuracy of testing. - **Input Voltage and Power Supply**: The input voltage is usually AC 220V 50Hz, which is the standard power supply voltage in most countries and regions. At the same time, the tester is usually equipped with a stable power supply system to ensure voltage stability and accurate data during the testing process. - **Appearance Dimensions and Weight**: The appearance dimensions and weight of the tester may vary depending on the model and brand, but it is usually compact and portable. This enables the tester to be used in different production sites and laboratories, improving the convenience and flexibility of testing. - **Working Environment**: The tester usually needs to be used in a certain working environment, such as a working temperature between 23°C±2°C and a relative humidity not exceeding 80% (without condensation). These working environment requirements can ensure the normal operation of the tester and the accuracy of test results.
Leave Message Get Price