Vertebral Fixation Plate Fatigue Tester
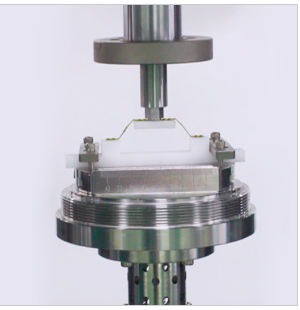
Standards:
ASTM F1717
ASTM F2706
ISO 12189
Main applications:
Performance evaluation: Test the fatigue performance of vertebral plate fixation plate systems under different loading conditions, including indicators such as yield load, stiffness, and durability.5 By applying cyclic loads that simulate the bending, axial, or combined stresses experienced by the plate system in the spine, the tester determines how many cycles the construct can withstand before fatigue failure. This provides crucial data on the system's fatigue strength and its ability to maintain structural integrity over its intended lifespan.6
Quality control: During the production process, use the fatigue tester to conduct quality inspections on vertebral plate fixation plate systems.7 By subjecting samples from each manufacturing batch to fatigue testing according to established criteria (e.g., survival for a specified number of cycles at a given load level), manufacturers can ensure that each batch of systems meets the predetermined performance standards for fatigue resistance.8 This is vital for maintaining consistent product quality and reducing the risk of implant failure in patients.
R & D support: Provide experimental data support for the research and development of vertebral plate fixation plate systems, helping R & D personnel optimize system design, materials, and manufacturing processes, and improve their durability and stability. Testing different plate geometries, screw types, material alloys, and surface treatments under fatigue conditions helps engineers understand their impact on performance and guides the development of more robust and long-lasting vertebral fixation systems.
Product Advantages:
The Vertebral Fixation Plate Fatigue Tester offers significant advantages for assessing the crucial fatigue performance of vertebral fixation plate systems:
Simulates Spinal Loading: Replicates the complex cyclic loads, particularly bending fatigue, experienced by vertebral plates in the spine.
Provides Crucial Fatigue Data: Determines the fatigue life and resistance to failure under repetitive loading, essential for predicting implant longevity and preventing fracture.9
Critical for Patient Safety: Contributes directly to ensuring the long-term mechanical integrity of the spinal construct, reducing the risk of implant failure and associated complications.
Supports Regulatory Compliance: Enables testing according to standards required by regulatory bodies (like FDA) for spinal implant assemblies and vertebral fixation devices.
Objective Performance Comparison: Provides a standardized method for objectively evaluating and comparing the fatigue performance of different vertebral plate system designs, materials, and manufacturers.
Facilitates R&D and Quality Control: An indispensable tool for developing improved plate systems and for maintaining consistent manufacturing quality.
Product Features:
A Vertebral Fixation Plate Fatigue Tester is typically a dynamic testing system capable of applying controlled cyclic loads to vertebral fixation plate systems. The specific configuration depends on the type of loading being simulated (most commonly bending fatigue). Key features include:
A dynamic testing frame (e.g., servo-hydraulic or electrodynamic) with the capacity and stiffness required to apply physiological loads and displacements over millions of cycles.
A specialized fixture designed to hold the vertebral fixation plate system in a configuration that simulates its attachment to vertebrae and allows for the application of cyclic loads. This often involves attaching the plate to simulated vertebral body models (e.g., rigid polyurethane foam or bone models) using bone screws, and then applying bending or other relevant fatigue loads to the construct.
Dynamic load cell(s) for accurate measurement of the applied cyclic force(s).
Displacement sensor(s) to measure the deformation of the plate system or construct under cyclic loading.
Advanced control system capable of applying various cyclic waveforms at specified frequencies and load or displacement amplitudes, potentially including multi-axial loading capabilities to better simulate complex spinal mechanics.
A cycle counter to accurately record the total number of load cycles applied.
A data acquisition system to capture load, displacement, cycle count, and potentially other relevant data throughout the fatigue test.
Sophisticated software for setting up fatigue test parameters, real-time monitoring of test progress, detecting sample failure (e.g., plate fracture, screw loosening), and analyzing fatigue data (e.g., generating S-N curves, evaluating stiffness degradation).
An environmental chamber or fluid bath designed to enclose the test setup, capable of maintaining physiological temperature (e.g., 37°C) and holding a simulated body fluid (e.g., saline solution) to replicate the in vivo environment.
Safety features such as overload protection, emergency stops, and protective enclosures.
Technical Parameters:
Dynamic Load Capacity: (e.g., typically ranging from ±5 kN to ±25 kN or more, depending on the expected loads applied to the plate construct)
Frequency Range: (e.g., up to 10 Hz, 20 Hz, or higher, as specified by the relevant testing standard, typically around 5-10 Hz for spinal fatigue tests)
Load Control Accuracy: (e.g., ±1% of set load or better)
Displacement Control Accuracy: (e.g., ±1% of set displacement or better)
Type of Loading: (Most commonly bending fatigue, but potentially also axial or combined loading depending on the test standard and application)
Maximum Number of Cycles: (Designed for long-term testing, e.g., up to 5 million or 10 million cycles as per standards)
Actuator Stroke: (Sufficient to apply required displacements under cyclic loading)
Environmental Chamber/Fluid Bath Temperature Range: (e.g., Ambient to 40°C or higher, with precise control around 37°C)
Environmental Chamber/Fluid Bath Temperature Accuracy: (e.g., ±1°C or ±0.5°C)
Sample Size Capacity: (Able to accommodate various vertebral plate designs, sizes, and configurations with bone screws and simulated vertebral bodies)
Power Supply: (e.g., AC 220V or 380V, 50/60 Hz, potentially with a hydraulic power unit if servo-hydraulic)
Leave Message Get Price