Oxide film abrasive tester
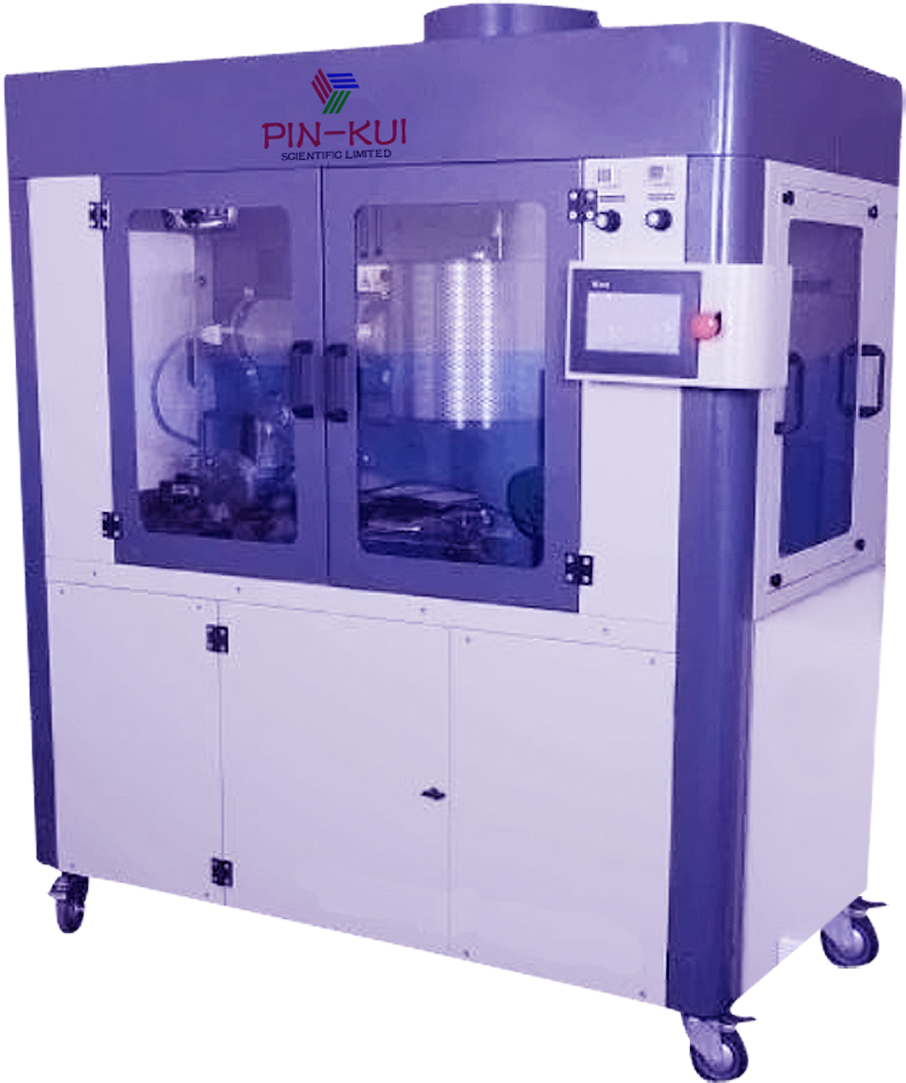
Applicable standards:
GB/T 12967: This standard specifies in detail the test method for determining the average wear resistance of aluminum and aluminum alloy anodized films with a spray grinding tester, and is suitable for the inspection of all oxide films with film thickness not less than 5μm. This standard is particularly applicable when testing small specimens (such as specimens with a diameter of 2mm) or specimens with uneven surfaces is required.
Main parameters:
Abrasive pressure: refers to the pressure generated by the jet flow on the specimen surface. This parameter has a significant impact on test results and therefore needs to be adjusted according to specific test requirements and material characteristics. Generally speaking, the spray grinding pressure is adjustable within a certain range to ensure the accuracy and reliability of the test.
Sand-blasting speed: refers to the speed at which abrasive particles are sprayed to the surface of the sample by the sand-blasting device. This parameter also has an important impact on the test results. Common blasting speeds can range from 20g/min to 30g/min, but specific values can vary by tester model and manufacturer.
Nozzle diameter: The diameter of the nozzle determines the cross section area and flow rate of the jet stream, which in turn affects the spraying effect of the abrasive. The choice of nozzle diameter should be determined according to the test requirements and material characteristics to ensure the accuracy of the test results.
Abrasive type and particle size: Abrasive is one of the key factors in the spray grinding test. Common types of abrasives include silicon carbide particles, quartz sand, etc. The particle size of the abrasive has a significant impact on the test results, so it needs to be selected according to the specific test needs. Generally speaking, the finer the abrasive particle size, the longer the test time; The coarser the abrasive particle size, the shorter the test time.
Jet Angle: refers to the Angle between the jet stream and the specimen surface. This parameter has a certain impact on the test result, so it needs to be calibrated and adjusted before the test. A common injection Angle may be around 45°, but the exact value may vary by tester model and manufacturer.
Test time: refers to the duration of the abrasive test. The length of the test time depends on a number of factors, such as abrasive type, particle size, blasting pressure, blasting speed, and the characteristics of the sample material. During the test, it is necessary to pay close attention to the wear of the sample and stop the test in time to avoid excessive wear.
Sample size: The size and shape of the sample have a certain impact on the test results. Therefore, before testing, it is necessary to prepare suitable samples according to the specific test requirements and the requirements of the tester. Common specimen sizes may include square specimens with a side length of 40mm to 50mm and a thickness of not less than 5mm.
Leave Message Get Price